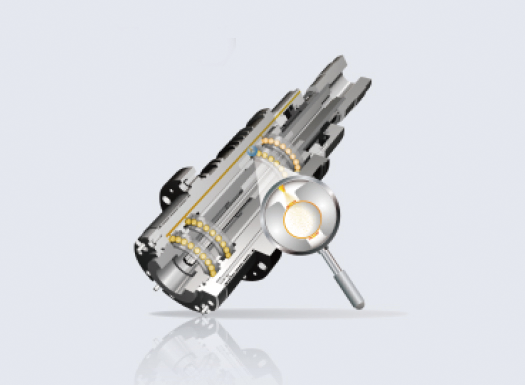
High efficient spindle
Box Guideways Hybrid Air Suspension and Environment Thermal Displacement Compensation
Improved machine accuracy
1. Box Guideways Hybrid Air Suspension: Quadrant error reduced by 50%, 30% reduction in backlash error.
2. Spindle run-out within 5μm.
3. Double column below 6 meters, machine thermal displacement can be reach within 0.03mm.