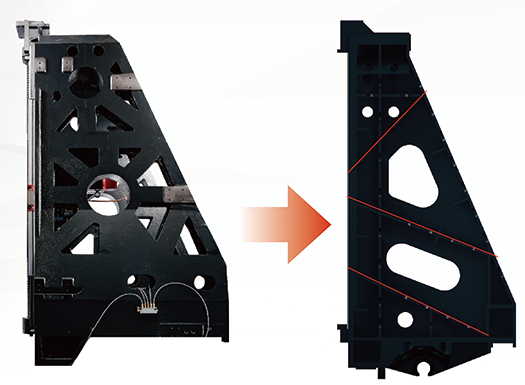
HMC series with high performance spindle
Fantastic performance for any machining application
1. One-piece design on column, 25% wider width, 15% rigidity increased, T-shape base features high stability, specially design on guideways, distance between linear guideways is 580mm; inside the casting are the anti-flex, vibration-absorbing ribs, makes the machine perfect for heavy-duty cutting.
2. Unique V-ribs delivers solid structure for horizontal machining center.